Tetra Pak has launched an initiative dubbed ‘Factory Sustainable Solution’ which seeks to advance sustainability across the entire food and beverage (F&B) manufacturing industry.
The approach has been designed to assist its customers to reduce their energy and water consumption significantly while also optimising critical Cleaning in Place (CIP) processes.
Tetra Pak, which was established in 1952, is the global leader in food processing and packaging solutions and works closely with its customers and suppliers on food safety.
The comprehensive and factory-wide approach integrates state-of-the-art technologies and expert plant integration capabilities that are tailored to the needs of individual customers.
The firm says the move tackles the need for F&B producers to enhance the use of resources amid increasing operational costs, strict CO2 taxes, and demand for more efficient practices.
Read More
“We know that our customers are under pressure more than ever to operate as efficiently as possible when it comes to resource usage,” said Tetra Pak Vice President Key Components, Plant Solutions and Channel Management Fiona Liebehenz.
Liebehenz noted that the need to operate efficiently in resource utilisation poses a serious challenge to many companies globally in their efforts to secure the future of their operations.
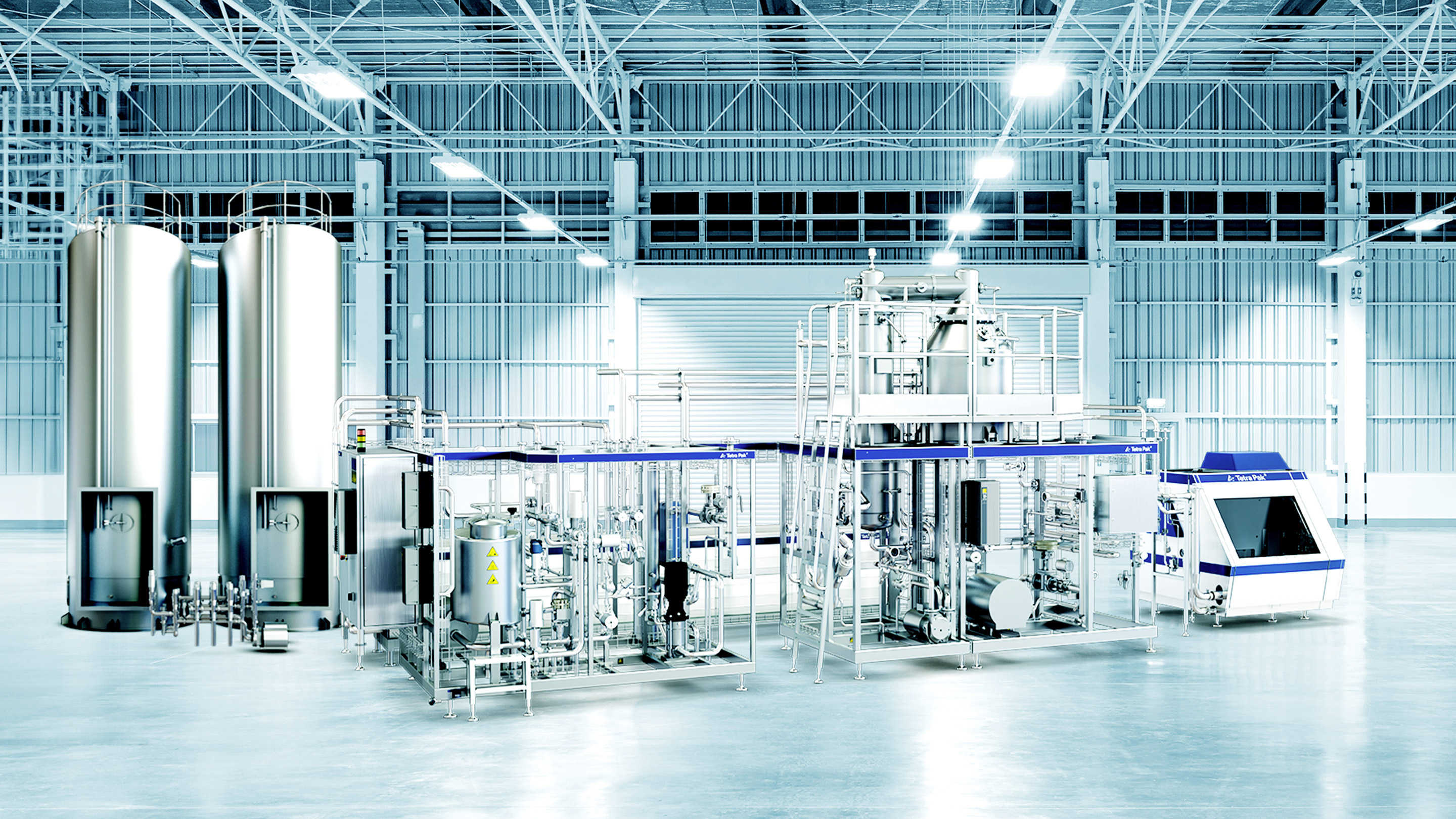
“Through working with them and understanding their individual needs and objectives, we’re providing fit-for-purpose equipment enriched with our holistic food and beverages application knowledge to address that challenge, delivering tangible improvements in a way that is financially advantageous,” she added.
Among the cutting-edge technologies incorporated into the mega company’s ‘Factory Sustainable Solutions’ approach suite are:
• Nanofiltration: This technology allows for up to 90 per cent recovery of spent CIP liquids, reclaiming clean detergent chemicals and water for reuse.
• Reverse Osmosis: Utilising proprietary membrane filtration, this method enhances resource efficiency across various applications, from milk separation to water reuse.
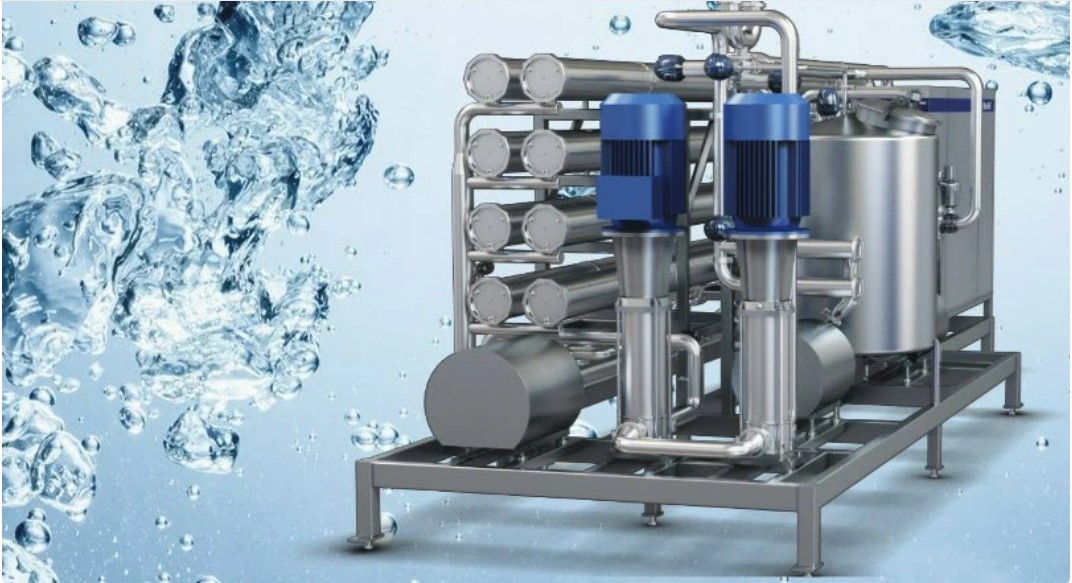
Tetra Pak is also collaborating with a number of innovative technology partners to offer additional solutions through the initiative, including:
• HighLift™ Heat Pump Technology: Developed with Olvondo Technology A/S, this technology repurposes waste heat to produce steam at high pressures, suitable for UHT applications.
• High-Temperature Heat Pumps: In partnership with Johnson Controls, these pumps up-cycle process waste heat for use across the factory.
• Solar Thermal Collectors: Working with Absolicon, this solution harnesses solar energy to deliver hot water and steam, contributing to the use of clean and renewable energy sources.
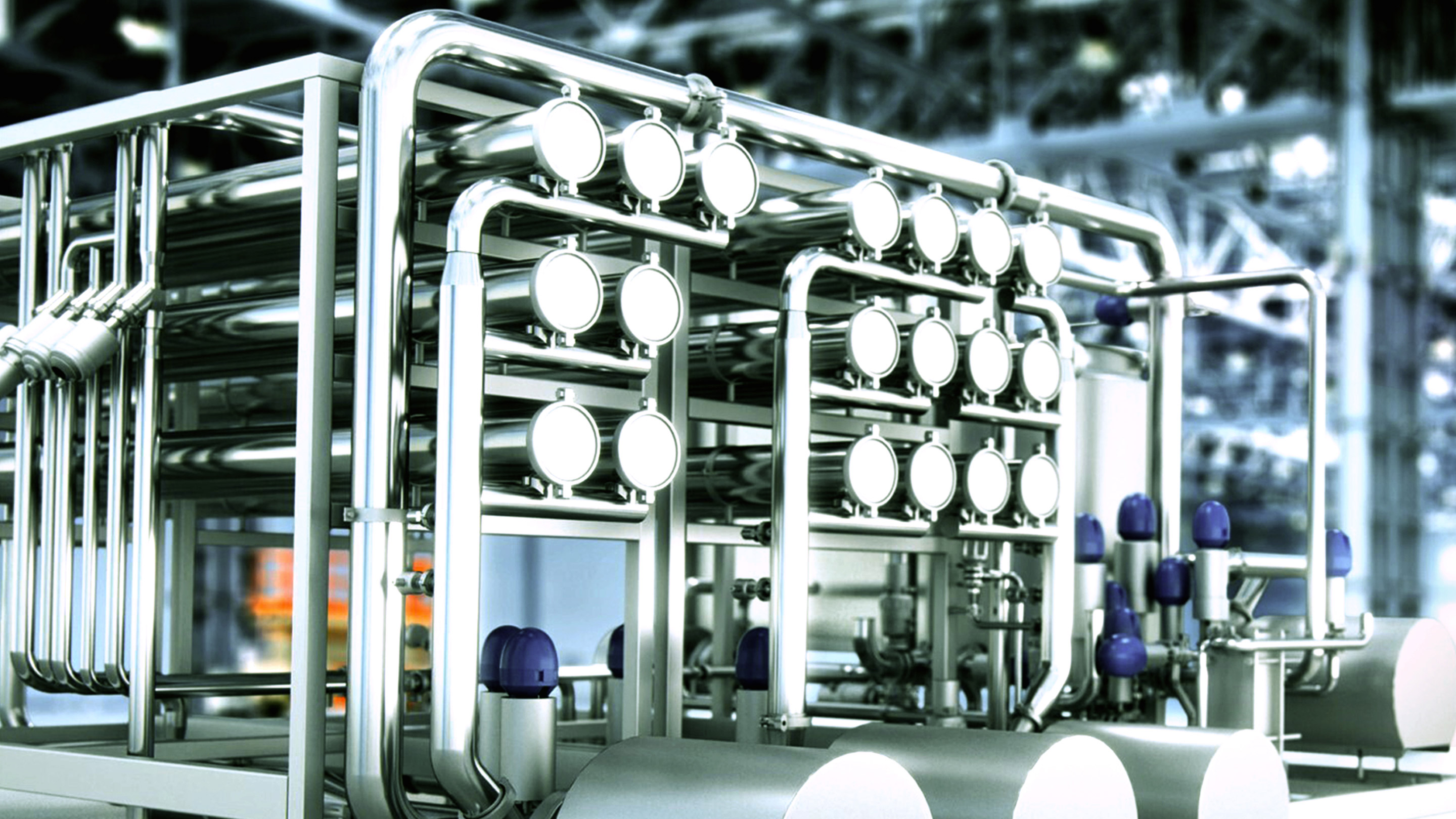
Tetra Pak Director of Factory Sustainable Solutions and OEM Components Nicole Uvenbeck applauded the new initiative terming it a milestone for the F&B industry across the globe.
“To date, we have mainly focused on machine and line optimisation, and we came to realise the overwhelming benefit of replicating this at a factory level, providing a more holistic approach to optimization,” explained Nicole.
“Factory Sustainable Solutions’ is an evolution of our expertise, spanning water, energy and CIP recovery.
“All of this combined will redefine how we support our customers in achieving their sustainability ambitions, while reducing their operational costs.”
Tetra Pak is a Swedish multinational company headquartered in Switzerland and specialises in food packaging and processing.
It offers packaging, filling machines and processing for dairy, beverages, cheese, ice cream and prepared food, including distribution tools including accumulators, cap applicators, conveyors, crate packers, film wrappers, line controllers and straw applicators.
Tetra Pak was founded by Ruben Rausing and built on Erik Wallenberg's innovation, a tetrahedron-shaped plastic-coated paper carton, from which the firm’s name was derived.